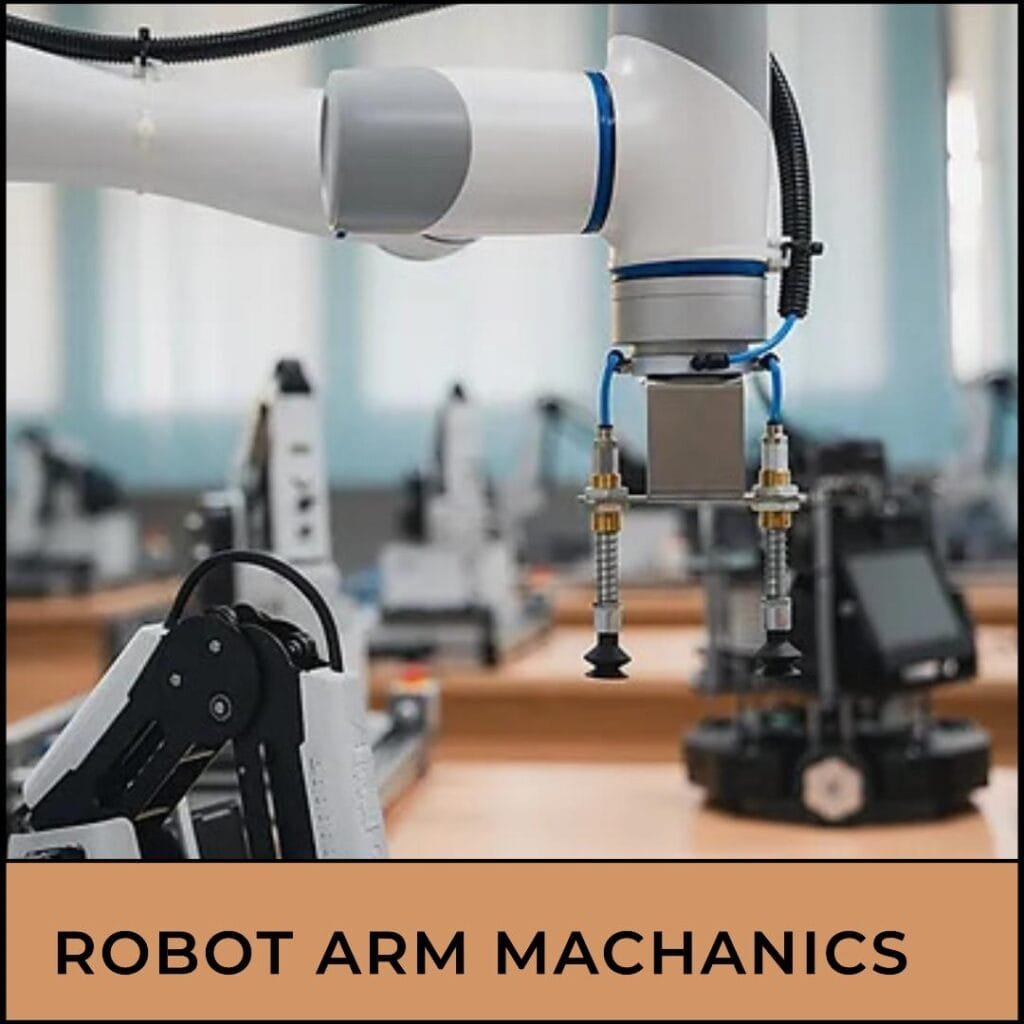
With the robotic arm among the most often utilized and flexible kind of robots, the development of robotics has revolutionized many different sectors. Robotic arms, which replicate the range of motion of the human arm, can be employed for jobs requiring great accuracy, strength, or repeated motions. Fascinating robot arm machanics involve sophisticated designs and control systems to guarantee stability, accuracy, and functionality.
1. Anatomy of a Robotic Arm
Usually with segments for the base, shoulder, elbow, wrist, and end effector, robotic arms are built like human arms. Every part has a specific function and is linked to one another via joints that permit movement in several directions.
- Base: The stationary or rotational base serves as the foundation for the arm, providing stability.
- Shoulder and Elbow Joints: These connect the main segments, allowing the arm to extend, retract, and lift.
- Wrist: Allows for more intricate movements, such as rotating and tilting the end effector.
- End Effector: The “hand” or tool at the end of the arm. It can be designed for gripping, welding, assembling, or manipulating objects.
2. Types of Robotic Arm Configurations
Robotic arms come in several configurations, each suitable for specific applications:
- Cartesian (Gantry) Arm: Moves in linear directions (X, Y, Z) and is typically used in pick-and-place applications.
- SCARA (Selective Compliance Articulated Robot Arm): Provides lateral movement with flexible vertical motion, ideal for assembly tasks.
- Articulated Arm: Most similar to a human arm, with multiple joints that allow high versatility and maneuverability.
- Delta Arm: Known for speed and precision, it consists of parallel arms connected to a stationary base, suitable for fast, delicate operations.
- Cylindrical Arm: Offers rotational and vertical movements in a cylindrical space, often used in welding and material handling.
3. Joints and Degrees of Freedom (DOF)
Usually determined by the number of joints, degrees of freedom (DOF) are the number of independent movements a robotic arm may generate.
- Rotary Joints (Revolute): Allow rotation along an axis. Common in wrist and elbow segments, they enable the arm to pivot.
- Prismatic Joints: Enable linear motion, which allows the arm to extend or retract in a straight line.
- Spherical Joints: Provide both rotational and angular movements in multiple planes, enabling a wide range of motion for intricate tasks.
An arm’s total degrees of freedom impact its versatility, with 5 to 7 DOF being common in industrial applications.
4. Motors and Actuators
Motors and actuators are essential to generate the movements required by the robotic arm.
- Servo Motors: Common in exact uses, servo motors provide precise control of joint angles. Feedback systems included in them guarantee that the posture corresponds with the aim.
- Stepper Motors: Ideal for applications needing repeated motions but not high-speed accuracy, move in discrete stages.
- Pneumatic and Hydraulic Actuators: Provide strong forces and are often used in heavy-lifting applications. However, they may be less precise than electric motors.
- Brushless DC Motors: Fit for high-performance robotic arms, offer great torque and extended life with low maintenance.
5. Sensors and Feedback Mechanisms
Sensors play a critical role in enabling a robot arm machanics to interact intelligently with its environment and ensure precise movement.
- Position Sensors (Encoders): Measure joint angles or linear positions, ensuring the arm moves accurately to the desired location.
- Force and Torque Sensors: Detect external forces and torques, protecting the arm from damage by adjusting its movements based on sensed feedback.
- Proximity Sensors: Used for collision avoidance and detecting nearby objects.
- Vision Systems: Cameras and image recognition systems allow the arm to identify and manipulate specific objects, enhancing adaptability in dynamic environments.
- Temperature Sensors: Monitor motor and actuator temperatures to prevent overheating.
6. Control Systems and Programming
The brain of a robotic arm is what coordinates motions and guarantees exact task execution.
- Direct Control vs. Motion Control: Direct control systems respond directly to commands, while motion control systems calculate optimal paths, enhancing precision.
- Inverse Kinematics (IK): Essential in calculating the required joint angles to reach a target position. IK enables the control system to handle complex movements across multiple joints.
- Trajectory Planning: Defines a path for the arm to follow, which helps avoid obstacles and ensures smooth motion. Applications needing great accuracy depend on this.
- Programming Languages: Languages include Python, C++, and specialist robotics languages like RAPID (for ABB robots) or KRL (for KukA robots) are commonly used in programming robot arms. Additionally supported by some robotic arms are block-based visual programming.
7. Types of End Effectors and Their Applications
The end effector is the part of the robotic arm that interacts with objects, and it can be customized for different tasks.
- Grippers: Used for picking and placing tasks. They can vary in design (parallel, angled, magnetic) based on the material and shape of the objects.
- Welders: Used in welding applications, where a robotic arm performs spot or arc welding.
- Screwdrivers and Drills: Common in assembly lines, these tools are used to fasten components together.
- Vacuum Suction Cups: Suitable for picking up flat objects, often used in packaging and materials handling.
- Cutting Tools: Used in manufacturing and processing industries, where cutting or trimming is required.
8. Power Supply and Energy Efficiency
Robotic arms depend on a consistent power source for continuous operation, hence power management is absolutely important for efficiency.
- AC and DC Power Sources: While AC power is common in industrial settings, DC power is often preferred in mobile or collaborative robots.
- Battery Power: Used in autonomous robots, although battery-powered arms may need to be optimized for energy efficiency.
- Regenerative Braking: Some advanced robots can recover energy during braking, which is especially useful in high-energy applications.
9. Applications of Robotic Arms
Robotic arms are widely used across industries due to their versatility and adaptability.
- Manufacturing: Used for assembly, welding, painting, and quality inspection.
- Healthcare: Assisting in surgeries, rehabilitation, and even in prosthetics to enhance patient mobility.
- Warehousing and Logistics: Automating pick-and-place tasks, sorting, and packaging in fulfillment centers.
- Agriculture: Tasks like fruit picking and soil analysis.
- Space Exploration: Robotic arms have been used on the International Space Station and rovers on Mars, where precision and reliability are paramount.
- Food and Beverage: Used in packaging, sorting, and sometimes in cooking and food preparation.
10. Challenges and Future Developments
Despite their advantages, robotic arms face several challenges that developers are working to overcome.
- Precision in Dynamic Environments: While robotic arms perform well in controlled environments, developing robust algorithms for uncertain or dynamic environments is an ongoing challenge.
- Cost and Accessibility: Advanced robotic arms can be expensive. Researchers aim to make them more accessible to smaller businesses through modular designs and lower-cost materials.
- Energy Efficiency and Sustainability: Reducing the environmental impact of robotic arms, especially for large-scale operations, is becoming a priority.
- Human-Robot Collaboration: Collaborative robots (cobots) are designed to work alongside humans safely. Innovations in this area focus on improved safety sensors and adaptive programming.
Conclusion
Robotic arms—which can quickly, precisely, and efficiently complete tasks—have become essential in many different fields. Improved materials, more user-friendly interfaces, and even deeper integration of robotic arms with artificial intelligence as technology develops should all be anticipated. These developments would make robotic arms increasingly more flexible, effective, and easily available, therefore transforming our approach to automation in many different fields.